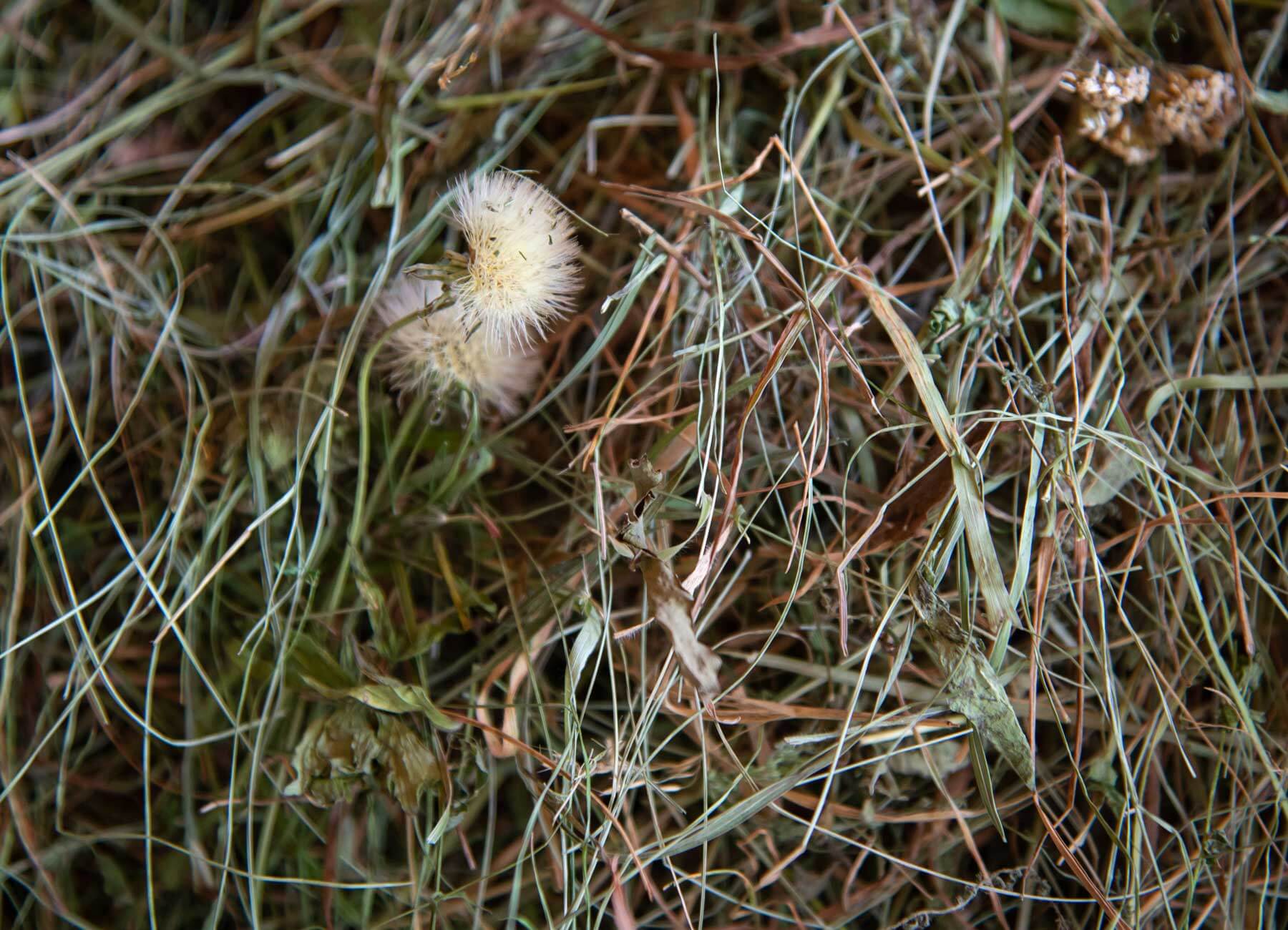
Conservation of the feed
Hay drying is a type of preservation, i.e. preservation of fodder – as with herbs or dried fruit. After successful drying, no more faulty fermentation or reheating takes place. The removal of water deprives bacteria and fungi of their basis of life and thus preserves the quality of the feed for many months. In addition to a maximum residual water content of 13% (87% dry matter), rapid drying of the feed within 70 hours (3 days) is crucial for successful preservation. From this time on, quality degradation occurs and only post-aeration should be necessary.
Post drying of the grass
The second advantage of technical drying is the possibility of bringing in moister forage, which would not be possible with cold ventilation or soil drying. As a result, crumb losses in the field can be largely avoided. The ideal residual moisture in the forage is 35% (65% dry matter) as a compromise between crumble losses and a very high energy consumption during drying. At more than 40% residual moisture (60% dry matter), drying costs increase disproportionately and even good drying plants run the risk of being overloaded.